Do You Understand USP 661.2 and Why It's Crucial for Packaging in the Pharmaceutical Industry?
Do You Understand USP <661.2> and Why It's Crucial for Packaging in the Pharmaceutical Industry?
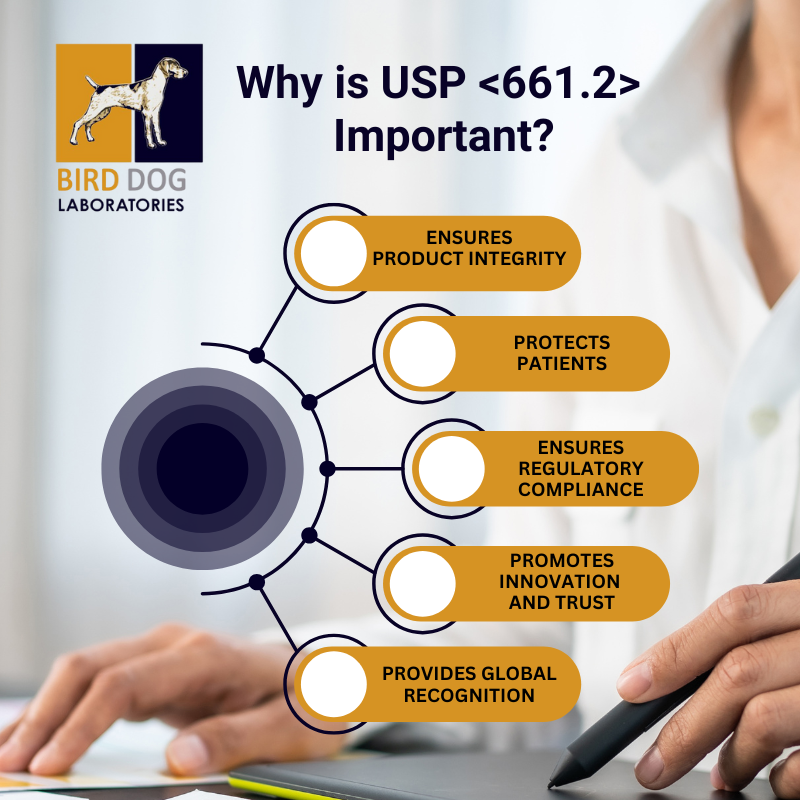
REMEMBER: The deadline for USP <661.2> is December 1, 2025. This is the date when USP <661.2> and USP <661.1> will replace USP <661> and become the new standards for plastic packaging and manufacturing materials used for pharmaceuticals.
In the world of pharmaceuticals, safety and quality are paramount. One key element ensuring that both are maintained is the United States Pharmacopeia (USP) standards, which provide guidelines for the quality, purity, and consistency of products. Among these, USP <661.2> stands out as an essential standard for the materials used in packaging pharmaceutical products. But what exactly is it, and why does it matter?
What is USP <661.2>?
USP <661.2> is part of the USP General Chapter 661 series, which addresses the requirements for plastic materials used in pharmaceutical packaging. Specifically, USP <661.2> focuses on the biological reactivity and potential leachability of substances from packaging materials into the drug product. It is designed to ensure that plastic materials, such as bottles, closures, and unit dose packages are safe for direct contact with pharmaceutical products and do not adversely affect the drug's safety or effectiveness. The chapter sets forth guidelines to test the interaction between packaging materials and the drug, evaluating factors like the potential migration of chemicals and other substances that could compromise the quality of the pharmaceutical product.
Why is USP <661.2> Important?
- Ensuring Product Integrity: Pharmaceutical packaging serves as a barrier between the drug and the outside environment, maintaining the product's potency, stability, and sterility. If packaging materials do not meet the standards outlined in USP <661.2>, there's a risk of contamination or degradation, which could affect the drug's efficacy and safety.
- Protecting Patients: The leaching of harmful substances from packaging materials can potentially harm patients. USP <661.2> ensures that materials used for packaging do not release toxic or harmful chemicals into the drug, safeguarding the health of consumers.
- Regulatory Compliance: Adherence to USP <661.2> is often required by regulatory bodies like the FDA. Pharmaceutical manufacturers must comply with these standards to ensure their products are marketable and meet safety requirements.
- Promoting Innovation and Trust: As the pharmaceutical industry evolves, new materials and packaging solutions are continually being developed. USP <661.2> provides a standardized framework for testing these materials, ensuring that innovative packaging options maintain the same level of safety and performance.
- Global Recognition: USP standards, including <661.2>, are recognized worldwide. Compliance with these guidelines not only ensures the quality of pharmaceutical packaging in the U.S. but also facilitates global trade by meeting international quality expectations.
Key Takeaways:
- USP <661.2> focuses on ensuring plastic materials used in pharmaceutical packaging are safe and do not negatively interact with the drug.
- USP <661.2> plays a crucial role in maintaining drug quality, safety, and efficacy.
- Compliance with USP <661.2> is vital for regulatory approval and maintaining trust with patients and healthcare providers.
In conclusion, USP <661.2> is a cornerstone in ensuring that the packaging of pharmaceutical products meets rigorous safety and quality standards. Its role in protecting both the integrity of the drug and the health of patients underscores its importance in the pharmaceutical industry. For manufacturers, compliance with this standard is not just a regulatory requirement, it's a commitment to producing safe, effective, and reliable products.
If you have questions regarding USP <661.2> or USP <671>, call Bird Dog Laboratories at 1-800-774-6061 or email mperkins@birddoglaboratories.com. Our team provides an assurance of accuracy and hyper-focused attention to detail for all packaging testing.
Recent Posts
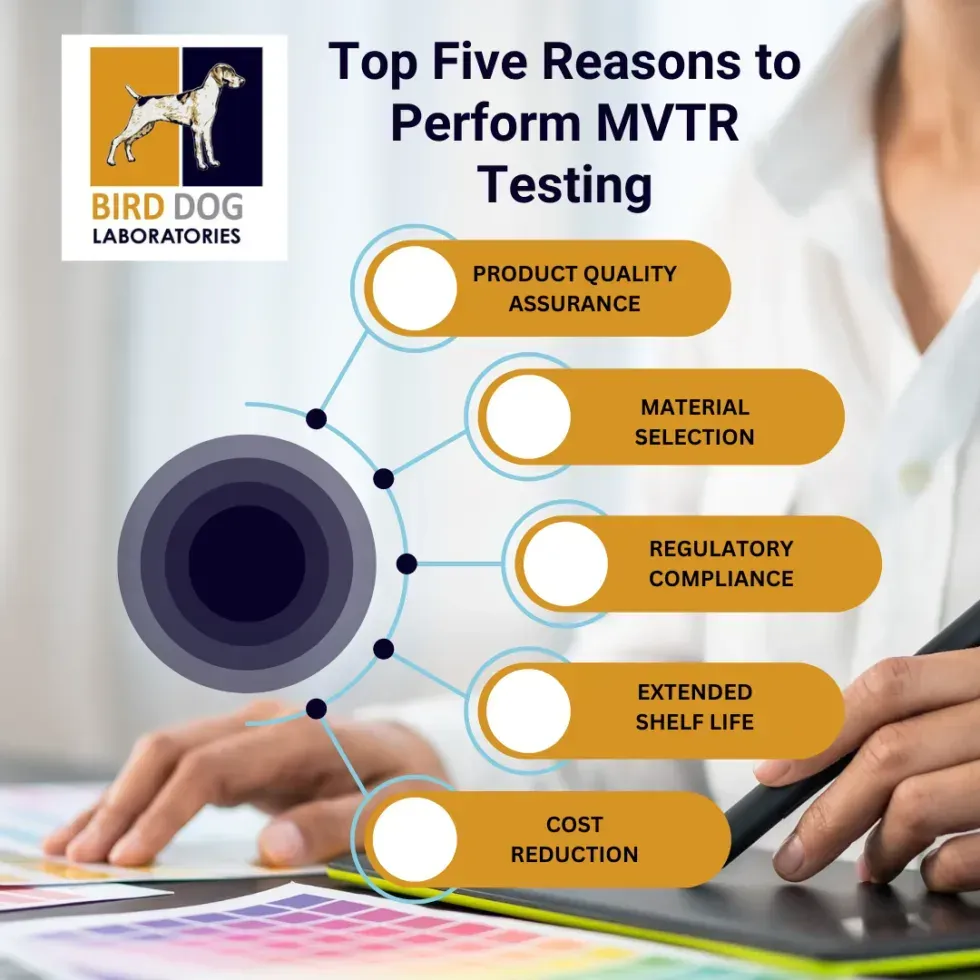
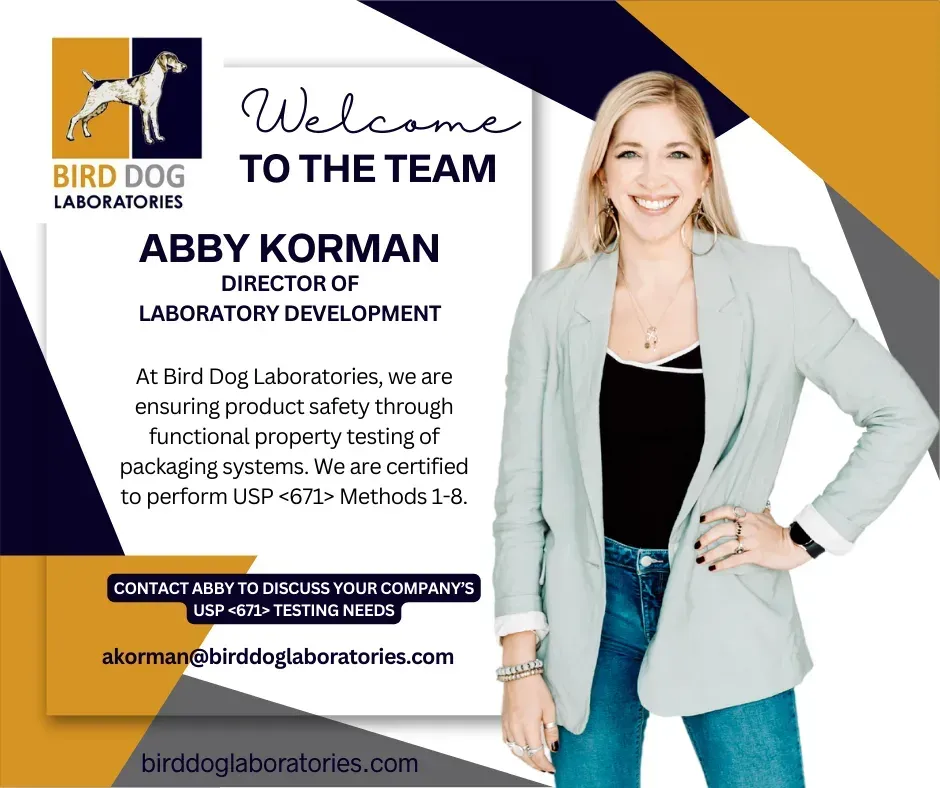